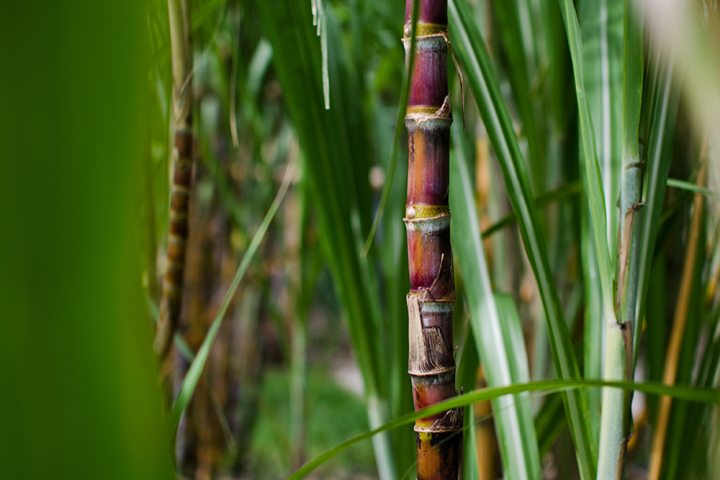
Biopolímeros: los brotes jóvenes se imponen
El mundo de los plásticos también se ha comprometido a aceptar el desafío ecológico de los próximos años. Los plásticos de origen vegetal han visto el surgimiento de innovaciones interesantes, algunas de las cuales presagian lo que serán los plásticos del futuro. ¡Repasemos los detalles!
El PLA mete el dedo en la llaga
El ácido poliláctico (PLA) es uno de los bioplásticos más antiguos, lo que explica, al menos en parte, por qué en la actualidad es la estrella indiscutible de los plásticos de origen vegetal. El PLA representa cerca del 20 % de los bioplásticos producidos en 2021. Su proceso de fabricación se basa en el ácido láctico, obtenido por fermentación de los azúcares (sacarosa, glucosa, etc.) presentes en las plantas (caña de azúcar, remolacha, etc.) o extraídos de su almidón (maíz, trigo, patatas, etc.). A continuación, se destila el ácido láctico y se polimeriza para convertirse en el ácido poliláctico. Este es compostable en las condiciones de compostaje industrial (por encima de 60º).
El PLA se utiliza mayoritariamente en los envases alimentarios (el 66 % de su producción), principalmente por sus propiedades de barrera (protección contra la oxidación) y porque su transparencia permite que los consumidores vean los alimentos. Es muy flexible y puede volverse rígido al añadir cal, en cuyo caso se llama PLA cristalizado. |
![]() El plástico biobasado estrella, el PLA, está muy presente en los envases alimentarios y en las impresoras 3D.. |
También forma parte de las bandejas, de las películas transparentes para alimentos, así como de vasos y tazas. Los cubiertos o las tapas de las tazas suelen ser más de PLA cristalizado. Estos embalajes se utilizan principalmente en la comida rápida para los alimentos con un periodo de conservación corto. Es algo que resulta bastante lógico, puesto que este polímero no es totalmente impermeable, lo que limita su utilización en la protección de productos de conservación prolongada. También se ha hecho un hueco en el mundo de las telas no tejidas (toallitas, fundas de pañales, etc.) y de los materiales utilizados en las impresoras 3D, principalmente porque su punto de fusión es más bajo que el de otros polímeros. También constituye el material principal de numerosas prótesis impresas en 3D. En cirugía, también entra en la composición de algunos hilos de sutura y, en la actualidad, se está estudiando su uso en endoprótesis. El PLA es completamente reciclable, pero todavía no se han desarrollado los canales...
El PHA en busca de su futuro
Los polihidroxialcanoatos (PHA) y los polihidroxibutiratos (PHB), cuyas técnicas de fabricación son muy similares, tienen, según los expertos, un futuro muy prometedor a pesar de su coste, todavía elevado.
Estos poliésteres de origen vegetal presentan una ventaja sobre el PLA, puesto que son biodegradables en el medio natural. También podrían prestar grandes servicios en el ámbito de la salud en el diseño de materiales reabsorbibles: hilos de sutura y cápsulas de sustancias activas, entre otras cosas. En 2020, la Unión Europea puso en marcha un gran programa de investigación transnacional con el fin de encontrar la «receta» para fabricar PHA a partir de la biomasa procedente de microalgas. El objetivo es el desarrollo de un PHA que sea competitivo y sostenible tanto desde el punto de vista medioambiental como económico. |
![]() El PHA es muy reciente y, sin ninguna duda, tiene un gran porvenir, principalmente en el sector médico, donde sus cualidades de biodegradabilidad son perfectas para diseñar materiales reabsorbibles, como los hilos de sutura. |
Mientras tanto, el gigante de la industria alimentaria Mars anunció el año pasado una asociación con el fabricante estadunidense de biopolímeros Danimer Scientific para el diseño de un embalaje de golosinas elaborado con PHA. Los primeros embalajes de este tipo deberían estar en los supermercados muy pronto...
El Rislan® ofrece resistencia
En 1947, Arkema comercializaba el Rislan®, un nuevo polímero basado en el aceite de ricino. Se trata de una poliamida 11 que compitió con el famoso nailon, desarrollado por la empresa estadounidense Dupont de Nemours. Su trayectoria es más que honorable. Gracias a su resistencia, se utiliza en cables, tubos de alta presión, etc. Incluso se ha convertido en un nombre genérico, puesto que los aficionados al bricolaje suelen llamar a las abrazaderas de plástico, un rislán. Por supuesto, por el nombre del material del que está fabricada. Y lo que resulta aún más extraordinario: este material que figura entre los «ancestros» de los plásticos biobasados modernos ha tenido éxito renovándose para figurar entre los polímeros más demandados. Al menos por los deportistas... En efecto, Arkema ha transformado este polímero en un elastómero termoplástico llamado Pebax®. Es ligero, elástico y resiste los golpes, y se utiliza en las suelas del calzado deportivo o en las botas de esquí. Como anécdota, Usain Bolt, el atleta triple medallista en los Juegos Olímpicos de Río en 2016 llevaba zapatillas equipadas con suelas de Pebax® de color verde a juego con su camiseta. Ni que decir tiene que en Arkema sus victorias fueron un poco suyas.
![]() El Rislan® ha ganado sus títulos de nobleza participando en la victoria de numerosos campeones olímpicos, como Usain Bolt |
El biopolietileno se azucara en el proceso
El polietileno (PE) es el material plástico más utilizado en el mundo. Su fabricación es barata, es polivalente y especialmente resistente, y encuentra aplicaciones en todos los sectores industriales: embalaje, construcción, automoción... Tradicionalmente se produce a partir de recursos fósiles, por polimerización del etileno. El etileno, el componente básico del material, puede obtenerse igualmente a partir del etanol obtenido a partir de la fermentación de las plantas ricas en azúcares (como la caña de azúcar, el maíz, etc.). La producción de caña de azúcar presenta la ventaja de ser menos perjudicial para el medioambiente que la remolacha azucarera o la del maíz, que necesitan más insumos y agua. El único inconveniente es que el coste de producción del bio-PE es superior al del PE obtenido a partir de petróleo. Ahora bien, diferentes estudios demuestran que los consumidores finales están dispuestos a pagar un poco más por sus productos si son de origen sostenible.
![]() La descarbonización obliga a que los fabricantes de juguetes se interesen cada vez más en los plásticos biobasados. |
El gigante del juguete, la empresa estadounidense Mattel, anunció hace poco su intención de elaborar todos sus productos a partir de polímeros biobasados o reciclados de aquí a 2030. |
Lego, el otro peso pesado del sector, declara ya desde hace varios años su intención de reemplazar el ABS de sus famosos bloques por un «polímero verde». Mientras tanto, ha optado por el bio-PE para todos los elementos botánicos de sus decorados (hojas de árboles, arbustos y troncos). Estos últimos no representan más que el 2,2 % de su producción.
Los famosos bloques no se ven afectados por el momento por el bio-PE, que no ofrece las mismas propiedades (brillo, solidez, indeformabilidad, etc.) que el ABS de su composición actual y que los convierte en casi indestructibles y completamente seguros para su uso por parte de los niños. Este es el motivo por el que la empresa ha invertido más de 130 millones de euros en un centro de investigación sobre los bioplásticos. |
![]() ¿Un guiño? Las hojas de los árboles de los productos de Lego son, en la actualidad, de bio-PE, un polietileno biobasado. |
El bio-PET está en alza
La caña de azúcar es también la preferida de los fabricantes del tereftalato de polietileno (PET) biobasado. Hasta hace poco, este PET solo estaba biobasado parcialmente. En efecto, se fabricaba a partir del mismo ácido tereftálico derivado del petróleo y de etilenglicol, que se suele fabricar a partir de la caña de azúcar. Cabe recordar que el PET es el material más utilizado en la fabricación de las botellas de bebida. Además, es un polímero que se recicla muy bien.
El bio-PET ha tenido un éxito fulgurante en los últimos años con el impulso de Coca-Cola que, desde finales de la década del 2000, lanzaba sus primeras botellas de bio-PET (el que todavía contiene el ácido tereftálico derivado del petróleo). La marca se había fijado como objetivo la producción de las botellas a partir de un ácido tereftálico 100 % de origen vegetal en la siguiente década. Esto pudo lograrse gracias a su asociación con la empresa estadounidense Virent, una empresa emergente especializada en biocombustibles.
La PlantBottle, su botella 100 % biobasada, se fabrica a partir de un paraxileno derivado de las plantas que se convierte en ácido tereftálico. Una primicia mundial que deberían seguir sus muchos competidores. En Europa y en Japón, Coca-Cola espera dejar de utilizar el PET de origen fósil de aquí a 2030. En estos países, la botella del futuro podría estar compuesta de un 70 % de PET reciclado mecánicamente y el resto de bio-PET. |
![]() Coca-Cola es la primera marca que ha comercializado una botella completamente biobasada. |
Al PVC no le falta sal
![]() El PVC biobasado tiene su origen en el residuo de la pasta de papel o en los aceites de cocina usados. |
El policloruro de vinilo (PVC) es también uno de los polímeros más utilizados en el mundo. Desde hace mucho tiempo es imprescindible en el sector de la construcción, donde forma parte de la composición de tubos, ventanas, puertas, cables eléctricos, revestimientos... Para producir el PVC son necesarias dos materias primas: el cloruro de sodio (de la sal marina o de cocina) y el etileno. Producir etileno verde a partir de plantas no es precisamente una novedad, pero lo que sí es novedoso en el contexto del PVC, es crearlo a partir de residuos de pasta de papel o del extracto de aceite de cocina usado. Aliaxis, uno de los líderes mundiales de los productos de canalización, ofrece en la actualidad una gama de tubos elaborada en un 50 % con PVC bio-atribuido* y el 20 % restante con PVC reciclado. El 30% restante se compone de rellenos minerales para garantizar el rendimiento acústico. Naturalmente, estos tubos presentan las mismas características técnicas que los de PVC tradicional. |
Bio-atribuido* : El PVC biobasado es 100% de origen no fósil. El PVC bio-atribuido permite la mezcla con una pequeña cantidad de material de origen fósil, basada en el principio de equilibrio de masas, consistente en residuos de aceite de cocina y pulpa de papel.