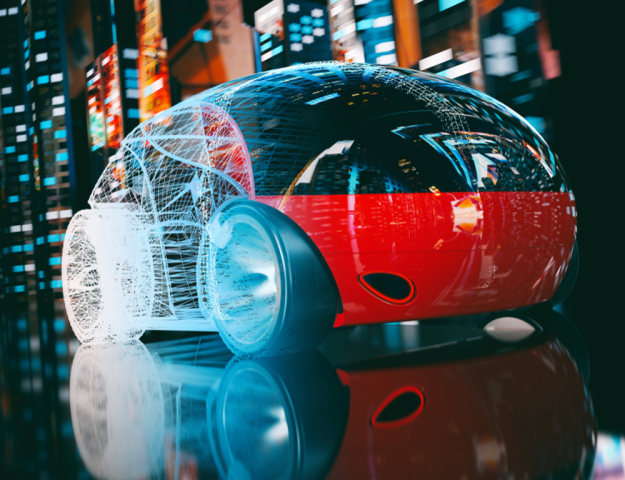
Los plásticos encabezan la carrera por reducir el peso de los automóviles
Polímeros: un plan de adelgazamiento eficaz
El sector de la automoción, un ámbito tan recurrente como fascinante, se encuentra de forma permanente bajo el foco de la prensa especializada, así como de las publicaciones sobre economía y tecnología. Aún más, si cabe, en este periodo de confinamiento sin precedentes que estamos viviendo a nivel mundial, en el que la venta de vehículos se ha desplomado hasta niveles extremadamente bajos. ¿Está en riesgo la continuidad de tales desarrollos debido al particular clima económico actual? ¿Significará el coronavirus el fin del cambio paradigmático que se está produciendo actualmente en el ámbito de la fabricación de vehículos? Sería una lástima, porque el sector está experimentando una verdadera revolución. En el espacio de tan solo una década, los fabricantes han cambiado radicalmente su visión sobre el coche del futuro.
Durante mucho tiempo, los fabricantes se centraron en lograr unos motores cada vez más potentes. Más tarde, con la llegada de la crisis del petróleo en los años 70, se buscó reducir el consumo de combustible. Las aplicaciones electrónicas, en ese momento ampliamente utilizadas para optimizar los motores, posibilitaron importantes mejoras en cuanto al consumo. Cuando se llegó al límite de lo que la tecnología podía ofrecer, la industria del automóvil decidió poner los vehículos a dieta para hacerlos menos «tragones».
![]() Los polímeros se convirtieron en el material indiscutible para el interior de los coches en la década de los 80. La facilidad con la que pueden moldearse y colorearse hizo realidad los sueños más osados. |
Empezaron entonces a fijarse en los materiales utilizados, especialmente en los polímeros, mucho más ligeros que los metales, que inicialmente se utilizaron para fabricar los interiores de los vehículos. Los esfuerzos invertidos pronto dieron sus frutos y la calidad percibida de los plásticos de a bordo se convirtió en un verdadero activo. Los plásticos rígidos dieron lugar a plásticos acolchados, suaves, con texturas o lisos. |
Desde entonces, los productores y fabricantes de materiales vienen ofreciendo de forma continua polímeros nuevos para seguir mejorando los productos, algunos de los cuales son ya insustituibles.
Pero lo que era posible en el interior no siempre lo era en el exterior. En la década de los 80, todas las marcas sin excepción instalaban parachoques de plástico. Una década más tarde, el fabricante francés Renault reemplazó el metal por poliamida en los guardabarros de las primeras generaciones de su modelo Clio. Fue también durante esa década cuando los fabricantes empezaron a tomar en consideración la huella ambiental de sus modelos utilizando plásticos reciclados. Se empezó tímidamente con piezas que con frecuencia se encontraban en zonas ocultas o poco visibles como, por ejemplo, los cárteres, los componentes de protección del motor o incluso las placas del umbral de la puerta. Peugeot, otro fabricante de automóviles francés, empezó en 2010 a equipar su modelo 208 con el primer parachoques hecho de un polímero reciclado.
Hoy en día, todos los fabricantes comparten un mismo objetivo: mejorar drásticamente su huella ambiental. No se trata simplemente de reducir las emisiones de CO2, ya que los motores de combustión interna emiten otros tipos de partículas tales como óxidos de nitrógeno. Por esta razón, las marcas están modificando gradualmente sus modelos para que utilicen energía eléctrica, a la vez que continúan reduciendo su peso.
![]() La entrada de los plásticos reciclados en el mundo de la automoción tuvo lugar en la década de los 90 y empezó de forma discreta. 20 años más tarde, PSA fue el primer fabricante que incorporó polímeros reciclados en uno de sus modelos de parachoques. |
Vehículos del futuro: los polímeros están a la altura
La conversión de los vehículos para que utilicen energía eléctrica es una de las principales preocupaciones de los fabricantes, especialmente de aquellos ubicados en Europa. Actualmente, están sujetos a sanciones muy elevadas si la flota vendida anualmente excede el umbral medio de 95 g de CO2/km* (hasta el 1 de enero de 2020, la referencia era de 130 g). En la actualidad, los vehículos eléctricos e híbridos representan aproximadamente el 6 % del total de ventas en Europa, y esta cifra ha seguido aumentando durante los últimos tres años. Sin embargo, todavía quedan obstáculos por superar. Los conductores siguen lamentando no poder utilizar su vehículo para realizar viajes largos. Y con razón, porque, aunque la red de estaciones de carga sigue creciendo de forma constante, todavía es bastante reducida. Encima, cargar un coche con electricidad no es como llenarlo de combustible. La carga de un automóvil requiere un mínimo de 30 minutos.
Por este motivo, los fabricantes tienen la prioridad de aumentar la autonomía de sus modelos eléctricos y dedican a ello todos sus esfuerzos. Las baterías son muy pesadas y ocupan mucho espacio, por lo que es imposible tener más de una batería a bordo. La historia se repite y los fabricantes vuelven a centrarse en los materiales que utilizan con el objetivo de hacer sus coches cada vez más ligeros. El criterio que se aplicaba para el combustible es aplicable también para la electricidad: cuanto más ligero es un vehículo, menos consume y menos energía necesita para moverse. Es un objetivo doble que implica hacer vehículos menos contaminantes y mejorar su autonomía.
Hace tiempo que los fabricantes saben cómo convertir un vehículo con motor de combustión en un vehículo eléctrico, aunque hasta hace poco simplemente retiraban el motor de combustión interna y lo reemplazaban por uno eléctrico. Las baterías solían instalarse en el maletero. Al tener una autonomía limitada, estos vehículos estaban destinados a circular por la ciudad y los adquirían principalmente las autoridades públicas. Eran vehículos que apenas satisfacían los objetivos medioambientales y no lograron persuadir a los millones de conductores para que hicieran la transición.
* Reglamento (UE) n°333/2014 del Parlamento Europeo y del Consejo, de 11 de marzo de 2014, por el que se modifica el Reglamento (CE) n°443/2009 a fin de definir las modalidades para alcanzar el objetivo de 2020 de reducción de las emisiones de CO2 de los turismos nuevos.
Como resultado, los fabricantes de automóviles cambiaron su enfoque y actualmente están diseñando vehículos que están verdaderamente optimizados para alojar un motor eléctrico y la capacidad de batería que este requiere. En menos de 10 años, la autonomía de los vehículos eléctricos ha aumentado considerablemente. |
![]() La reducción de peso sigue siendo uno de los puntos clave en el desarrollo de los vehículos eléctricos. El objetivo ya no es hacerlos más eficientes en cuanto al consumo de combustible y menos contaminantes, sino más autónomos. |
El bucle de los polímeros
Las piezas de la carrocería de los automóviles se hacen cada vez más de polipropileno; los cristales de los faros de policarbonato debido a su ligereza y resistencia; el ABS, los poliuretanos y los polietilenos se han instalado cómodamente en el habitáculo; y bajo el capó se utiliza la poliamida debido a su resistencia a las altas temperaturas. Aunque actualmente ya se hace un amplio uso de los polímeros, los fabricantes tienen el objetivo para las próximas décadas de reducir a la mitad el peso de sus vehículos.
La pregunta es... ¿cómo se puede seguir reduciendo el peso de un vehículo, en términos prácticos? No existe una respuesta sencilla a dicha cuestión, aunque la idea de una carrocería o una estructura de asiento hechas de resina polimérica y fibras de carbono resulta tentadora. Sin embargo, el coste sigue siendo un obstáculo. Por ahora, solo los fabricantes «premium» se han aventurado por ese camino. BMW, por ejemplo, ha diseñado una carcasa hecha de estos materiales para sus modelos eléctricos i3 e i8. Para lograrlo y a la vez lanzar un proceso industrial satisfactorio, el fabricante tuvo que diseñar un robot revolucionario capaz de pegar esas piezas de forma automática.
En el ámbito de la reducción de peso, los progresos se logran paso a paso, o mediante la implementación, como dirían los expertos en procesos industriales. En su gran mayoría, los plásticos implicados siguen siendo los mismos. Indudablemente, polímeros más nuevos como, por ejemplo, el PEEK, son prometedores debido a su resistencia a las altas temperaturas y su rigidez extrema, pero todavía se consideran demasiado caros.
![]() Los polímeros, por su parte, siguen evolucionando y, gracias a sus novedosas propiedades, se están haciendo un lugar en el diseño de motores. |
A pesar de ello, los ingenieros están estudiando más a fondo cada una de las piezas metálicas para ver si pueden reemplazarse por polímeros y se espera que esto de lugar a nuevos avances. En 2017, por ejemplo, el fabricante de accesorios Hutchinson fue galardonado con el Premio a la Innovación de la Sociedad de Ingenieros del Plástico por el éxito en la comercialización de unos soportes de motor hechos de un tipo de poliamida, que significaron la ruptura total respecto al aluminio utilizado hasta entonces. |
Las ventajas de estos nuevos soportes, unas piezas sujetas a un elevado estrés mecánico, se derivan, por supuesto, de su ligereza, pero también de la mejora en el aislamiento del habitáculo frente a vibraciones y sonidos. Con este conjunto de pequeñas mejoras no se ha llegado ni de lejos al final del camino, puesto que las firmas de diseño siguen trabajando en la concepción de los vehículos del futuro, y gracias, entre otros factores, a los polímeros, auguran una serie de espectaculares innovaciones.